A Deep Dive into the Electrical Conductivity of Copper Laminated Busbar
The Importance of Copper Laminated Busbar
Copper laminated busbar represents a critical element in the electrical systems utilized within rail vehicles. These busbars are crafted from numerous thin sheets or foils of copper that are layered with insulating materials, a design intended to significantly bolster both performance and reliability. The distinctive laminated structure markedly enhances electrical conductivity while effectively managing the heat produced during the flow of high currents.
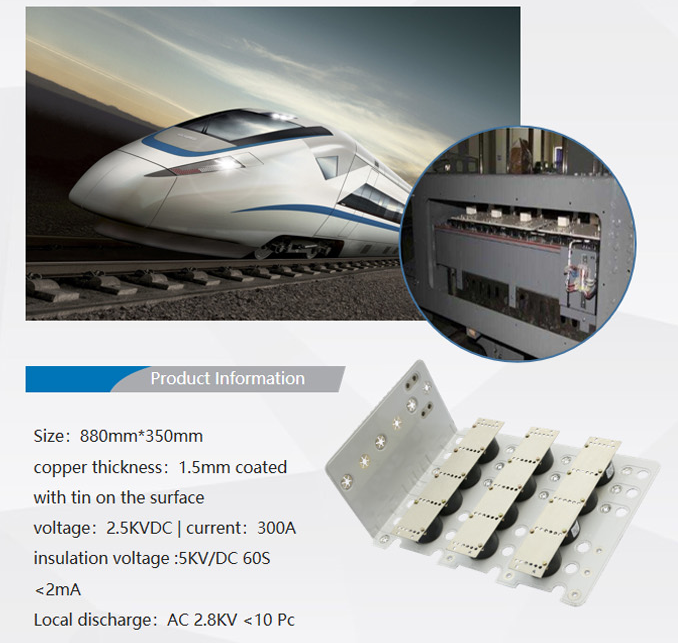
Within the framework of rail traffic, copper laminated busbar enables the efficient transfer of electrical power from the source to various vital components within the trains. These components encompass traction motors, lighting systems, control units, and other indispensable electrical devices. By providing a dependable power supply, these busbars play an essential role in maintaining the overall functionality and safety of rail systems.
The architectural design of copper laminated busbar facilitates a compact form factor, a characteristic particularly advantageous in the limited spaces of rail vehicles. This compactness not only conserves space but also enhances the overall efficiency of the electrical system, establishing these busbars as a preferred option for contemporary rail applications.
Electrical Conductivity and Performance
The Excellence of Copper’s Conductivity
Renowned for its superior electrical conductivity, copper serves as the optimal material for busbars tasked with managing high currents. The distinctive laminated structure inherent in these busbars permits them to optimize this conductivity while minimizing energy losses, a crucial factor in rail applications where power demands can fluctuate significantly during operation.
Moreover, the multi-layered construction of laminated busbars aids in the effective management of heat produced during electrical conduction. By distributing heat across several layers, these busbars mitigate the risk of overheating, which could otherwise result in failures within the electrical system. This capability in thermal management is vital for preserving the integrity and longevity of the electrical systems found in rail vehicles.
In addition, the design of copper laminated busbar allows for flexibility, enabling multiple input and output points. This versatility permits the tailoring of busbars to accommodate the specific needs of various rail systems, thereby enhancing their overall functionality and performance.
Cost-Effectiveness in Design
One of the most notable benefits of employing copper laminated busbar is their cost-effectiveness. When compared to traditional busbar designs, the laminated units necessitate significantly less assembly time, thereby translating to lower labor costs. Pre-manufactured laminated busbars can be installed swiftly, optimizing the entire assembly process.
Furthermore, the compact configuration of laminated busbars allows for efficient utilization of space, a factor of great importance in rail vehicles. By occupying minimal space while effectively conducting large currents, these busbars contribute to the overall optimization of the electrical system, paving the way for more efficient designs and layouts.
The long-term durability and reliability associated with copper laminated busbars further enhance their cost-effectiveness. With fewer failures and reduced maintenance requirements, operators can experience lower operational costs over time. This reliability positions laminated busbars as a prudent investment for rail operators aiming to enhance their electrical systems.
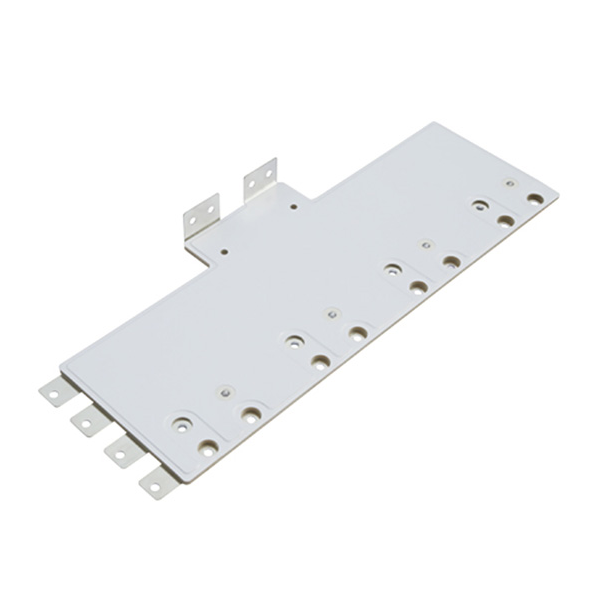
Proper Installation Techniques
Ensuring Optimal Performance
For copper laminated busbars to operate at peak efficiency, adherence to proper installation techniques is imperative. It is essential to ensure that all connections are securely made and that the busbar is appropriately positioned within the electrical system. Any misalignment or loose connections can lead to increased resistance, heat generation, and potential failures.
Prior to installation, comprehensive inspections must be performed to confirm that the busbars are undamaged and that all insulating materials remain intact. Such meticulous attention to detail during the installation phase can avert costly issues in the future, ensuring the safety and reliability of the entire electrical system.
Moreover, it is vital to follow manufacturer guidelines and best practices during the installation of copper laminated busbars. This includes utilizing the appropriate tools and materials to guarantee that the busbars are installed securely and correctly. Adhering to proper torque specifications when tightening connections is crucial to prevent damage to the busbar or adjacent components.
Adapting to Various Configurations
A standout attribute of copper laminated busbar is its remarkable adaptability to different configurations. Rail systems often exhibit significant variability in their electrical requirements, and laminated busbars can be engineered to accommodate these differences. This adaptability facilitates customized solutions that address the specific demands of each rail vehicle.
During the installation process, it is essential to consider the unique layout of the electrical system. This consideration may necessitate the creation of bespoke busbar designs that integrate seamlessly into the existing framework. By ensuring a precise fit, operators can optimize the efficiency of their electrical systems and enhance the overall performance of their rail vehicles.
Maintenance and Monitoring
Regular maintenance is vital for extending the lifespan of copper laminated busbar. The implementation of a monitoring system that includes signal acquisition points at various intervals along the busbar can assist operators in tracking performance and identifying issues early. This proactive methodology can substantially reduce the likelihood of unforeseen failures and prolong the operational life of the busbars.
Maintenance routines should encompass visual inspections, thermal imaging to identify hotspots, and electrical testing to verify that the busbars are functioning correctly. By prioritizing such maintenance, operators can significantly bolster the reliability of their rail systems while minimizing downtime.
The Future of Electrical Distribution in Rail
Emerging Trends in Busbar Technology
As the rail industry advances, so too does the technology associated with copper laminated busbar. Emerging trends encompass the incorporation of smart technologies that enhance monitoring and diagnostic functionalities. Such advancements enable real-time data collection and analysis, thereby improving decision-making processes and operational efficiency.
Additionally, innovations in materials and manufacturing techniques are propelling enhancements in busbar technology. New composite materials have the potential to improve the performance and durability of laminated busbars, providing even greater efficiency in electrical conduction and heat management. These developments are likely to play a significant role in shaping the future landscape of rail transportation.
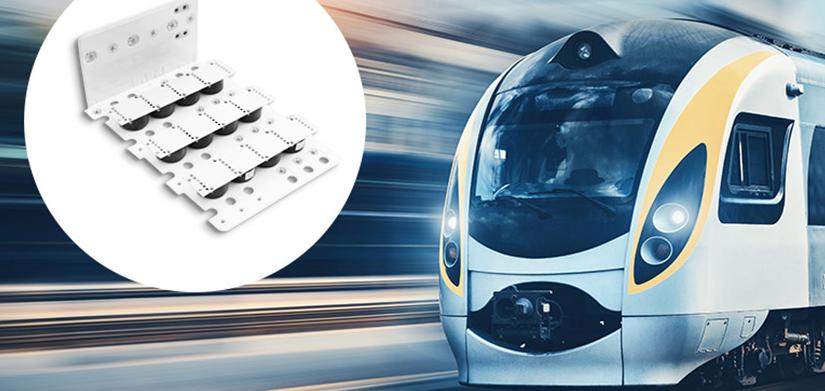
Furthermore, as rail systems strive for greater energy efficiency and sustainability, the demand for high-performance copper laminated busbars is anticipated to rise. These busbars are well-equipped to meet the requirements of modern rail systems, ensuring reliable and efficient power distribution.
The Role of Copper Laminated Busbars in Sustainability
Sustainability represents a critical consideration for the future trajectory of the rail industry. Copper laminated busbars contribute to this goal by enhancing energy efficiency and minimizing waste. Their capability to effectively transmit power with minimal losses allows rail operators to reduce overall energy consumption, thereby lowering carbon emissions.
Moreover, the durability of copper laminated busbar guarantees a longer lifespan when compared to traditional busbar designs. This longevity not only decreases the frequency of necessary replacements but also mitigates the environmental impact linked to the manufacturing of new components.
By investing in copper laminated busbars, rail operators can align their operations with sustainability objectives while concurrently improving performance and reducing costs.
Conclusion: The Integral Role of Copper Laminated Busbar
In summary, copper laminated busbar is an indispensable component within the electrical systems of rail vehicles. Their exceptional electrical conductivity, compact design, and cost-effectiveness render them a favored choice for contemporary rail applications. As the rail industry continues to evolve, the significance of reliable and efficient power distribution systems is poised to increase.
Shanghai Wenlida Technology Co., Ltd. emerges as a premier supplier of high-quality copper laminated busbars, dedicated to delivering innovative solutions that cater to the evolving demands of the rail industry. By embracing advancements in busbar technology, rail operators can enhance their electrical systems, optimize efficiency, and contribute to a more sustainable future.