What Makes Tin Plated Copper Laminated Busbar Stand Out in the Industry?
Uncover the versatile and dependable solution for optimal electrical conductivity with Tin Plated Copper Laminated Busbar. Delve into their wide-ranging applications across industries, spanning from renewable energy to telecommunications, and discover their exceptional conductivity, resistance to corrosion, and lasting durability. Assess their performance against alternative materials like aluminum or bare copper to make well-informed choices. Gain insights into maintenance techniques to uphold peak performance and extend longevity. Stay informed on the latest advancements propelling the development of Tin Plated Copper Laminated Busbar, driving forward sustainable energy solutions.
Introduction to Tin Plated Copper Laminated Busbar
1.1 Understanding Tin Plated Copper Laminated Busbar
Tin Plated Copper Laminated Busbar stands as a cornerstone in modern electrical systems. These busbars are engineered to efficiently conduct electricity while ensuring durability and resistance to corrosion. A tin-plated copper laminated busbar consists of multiple layers of copper sheets bonded together with tin plating on the surface. This construction provides superior electrical conductivity and mechanical strength, making them an essential component in various electrical applications.
1.2 Applications and Importance
The versatility of Tin Plated Copper Laminated Busbar finds applications across a spectrum of industries, including power generation, distribution, automotive, aerospace, and renewable energy systems. These busbars play a vital role in connecting different electrical components, ensuring smooth and uninterrupted power flow within systems. Their importance lies in their ability to handle high current densities efficiently while maintaining reliability and safety in critical operations.
Advantages of Tin Plated Copper Laminated Busbar
2.1 Enhanced Conductivity
Tin plating on the surface of copper laminated busbars significantly improves their conductivity. Tin, being a highly conductive metal, reduces the resistance of the busbar, resulting in minimal energy loss during transmission. This enhanced conductivity allows for the efficient transfer of electricity, reducing heat generation and optimizing the performance of electrical systems.
2.2 Corrosion Resistance
One of the most significant advantages of Tin Plated Copper Laminated Busbar is their resistance to corrosion. Tin plating acts as a protective layer, shielding the underlying copper from environmental factors such as moisture, humidity, and chemical exposure. This corrosion resistance ensures the longevity of the busbars, even in harsh operating conditions, thereby minimizing maintenance requirements and increasing the lifespan of electrical systems.
2.3 Durability and Mechanical Strength
The lamination process, combined with tin plating, imparts exceptional mechanical strength to copper busbars. This structural integrity allows them to withstand mechanical stress, vibrations, and thermal cycling without deformation or damage. The durability of Tin Plated Copper Laminated Busbar makes them ideal for use in high-power applications where reliability is paramount, ensuring uninterrupted operation under demanding conditions.
2.4 Real-World Applications
Tin Plated Copper Laminated Busbar finds extensive use in critical electrical systems where reliability and performance are non-negotiable. In power generation plants, these busbars are employed to connect generators, transformers, and switchgear, ensuring efficient power distribution. In the automotive industry, they are utilized in electric vehicles to transmit high currents between batteries, motors, and other components. Additionally, in renewable energy systems such as solar and wind farms, Tin Plated Copper Laminated Busbar plays a crucial role in transmitting power from the source to the grid.
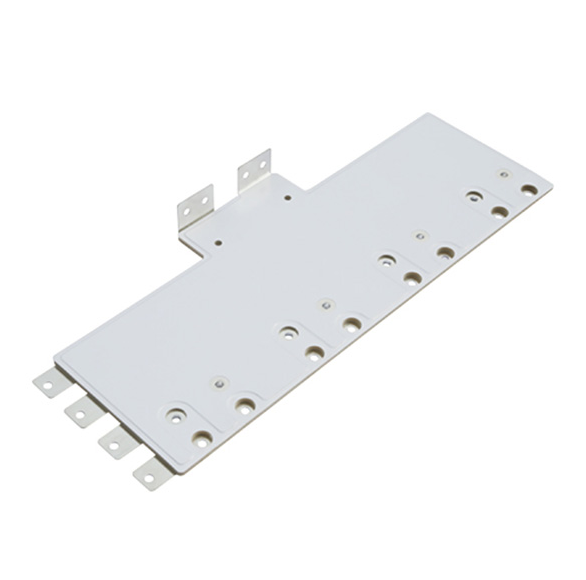
Manufacturing Process of Tin Plated Copper Laminated Busbar
3.1 Material Selection
The manufacturing process of Tin Plated Copper Laminated Busbar begins with the careful selection of high-quality copper sheets. The copper sheets must meet stringent criteria for conductivity, purity, and mechanical properties to ensure optimal performance of the busbars. Additionally, the tin plating material is selected for its corrosion resistance and compatibility with copper.
3.2 Bonding and Lamination
The selected copper sheets undergo a lamination process where they are bonded together to form a solid structure. This bonding process typically involves applying heat and pressure to the copper sheets, ensuring a strong and reliable bond between layers. The number of layers and thickness of the busbars can be customized according to specific application requirements, allowing for flexibility in design.
3.3 Tin Plating
After lamination, the surface of the copper busbars is coated with a layer of tin through electroplating or hot-dipping processes. Electroplating involves immersing the busbars in an electrolyte solution containing tin ions and applying an electric current to deposit tin onto the surface. Hot-dipping, on the other hand, involves dipping the busbars into molten tin to achieve the desired coating thickness. The tin plating provides corrosion resistance and enhances the conductivity of the busbars.
3.4 Finishing and Quality Control
Once tin plating is complete, the Tin Plated Copper Laminated Busbar undergoes finishing processes such as cutting, drilling, and surface treatment to meet specific dimensional and functional requirements. Rigorous quality control measures are implemented throughout the manufacturing process to ensure the integrity and performance of the busbars. This includes dimensional inspections, conductivity testing, and corrosion resistance evaluations to verify compliance with industry standards and customer specifications.
Innovations in Manufacturing
4.1 Advanced Bonding Techniques
Manufacturers like Wenlida employ advanced bonding techniques such as diffusion bonding and laser welding to enhance the strength and reliability of Tin Plated Copper Laminated Busbar. These techniques ensure a uniform bond between copper layers, minimizing the risk of delamination and improving the overall performance of the busbars.
4.2 Eco-Friendly Tin Plating Processes
In response to growing environmental concerns, manufacturers are adopting eco-friendly tin plating processes that minimize waste and reduce the use of hazardous chemicals. Innovations such as electrolyte recycling and alternative tin plating formulations help mitigate the environmental impact of tin-plated copper laminated busbar production while maintaining high performance and quality standards.
4.3 Customization and Rapid Prototyping
Advancements in manufacturing technology allow for the rapid prototyping and customization of Tin Plated Copper Laminated Busbar to meet the evolving needs of customers. Computer-aided design (CAD) software and precision machining equipment enable manufacturers to create intricate designs with precise tolerances, optimizing the performance and efficiency of electrical systems.
Comparative Analysis with Other Busbar Materials
5.1 Tin-Plated Copper vs. Aluminum Busbars
It offers several advantages over aluminum busbars, despite being more expensive. Copper has higher conductivity than aluminum, resulting in lower electrical resistance and reduced energy losses. Additionally, copper busbars exhibit superior corrosion resistance and mechanical strength compared to aluminum, making them more durable in harsh environments.
5.2 Tin-Plated Copper vs. Bare Copper Busbars
While both tin-plated and bare copper busbars share similar conductivity and mechanical properties, the tin plating provides added protection against corrosion. Bare copper busbars are susceptible to oxidation, which can degrade performance over time, especially in humid or corrosive environments. Tin-plated copper busbars offer enhanced longevity and reliability, making them a preferred choice for applications where corrosion resistance is critical.
5.3 Cost Considerations
Although Tin Plated Copper Laminated Busbar may have a higher initial cost compared to alternatives like aluminum or bare copper, their superior performance and longevity often justify the investment. The reduced maintenance requirements and extended lifespan of tin-plated copper busbars result in lower total cost of ownership over the long term, making them a cost-effective solution for many applications.
Maintenance and Care Tips for Tin Plated Copper Laminated Busbar
6.1 Cleaning and Inspection
Regular cleaning and inspection of Tin Plated Copper Laminated Busbar is essential to ensure optimal performance and prevent corrosion. Use a soft cloth or brush to remove dust and debris from the surface of the busbars, taking care not to scratch or damage the tin plating. Inspect the busbars for signs of corrosion, loose connections, or damage, and address any issues promptly to prevent further deterioration.
6.2 Corrosion Prevention
To prevent corrosion on the plated Copper Laminated Busbar, avoid exposure to moisture, humidity, and corrosive chemicals whenever possible. If installed in outdoor or corrosive environments, consider applying a protective coating or sealant to the busbars to provide an additional layer of protection against corrosion. Regularly monitor environmental conditions and take proactive measures to mitigate corrosion risks.
6.3 Troubleshooting Common Issues
If Tin Plated Copper Laminated Busbar experiences performance issues or electrical problems, conduct a thorough troubleshooting process to identify the root cause. Check for loose connections, damaged insulation, or overheating, and rectify any issues accordingly. If necessary, consult with a qualified technician or manufacturer for assistance in diagnosing and resolving complex problems.
Conclusion
Tin Plated Copper Laminated Busbar represents a cornerstone in modern electrical systems, offering enhanced conductivity, corrosion resistance, and durability. Their importance spans across various industries, where reliability and performance are paramount. With continuous advancements in manufacturing techniques and technologies, It is poised to play an even greater role in shaping the future of electrical engineering.